Smart product
Challenges
In industry and especially in the SME sector, many individual IT solutions can be found in order to ideally map one's own work processes. The provision of data requires a great deal of administrative effort in the individual companies. For the documentation of production and manufacturing processes and the associated transfer of information across factory and company boundaries, a unique identification of the component or assembly is also required.
Solution with IndustryFusion
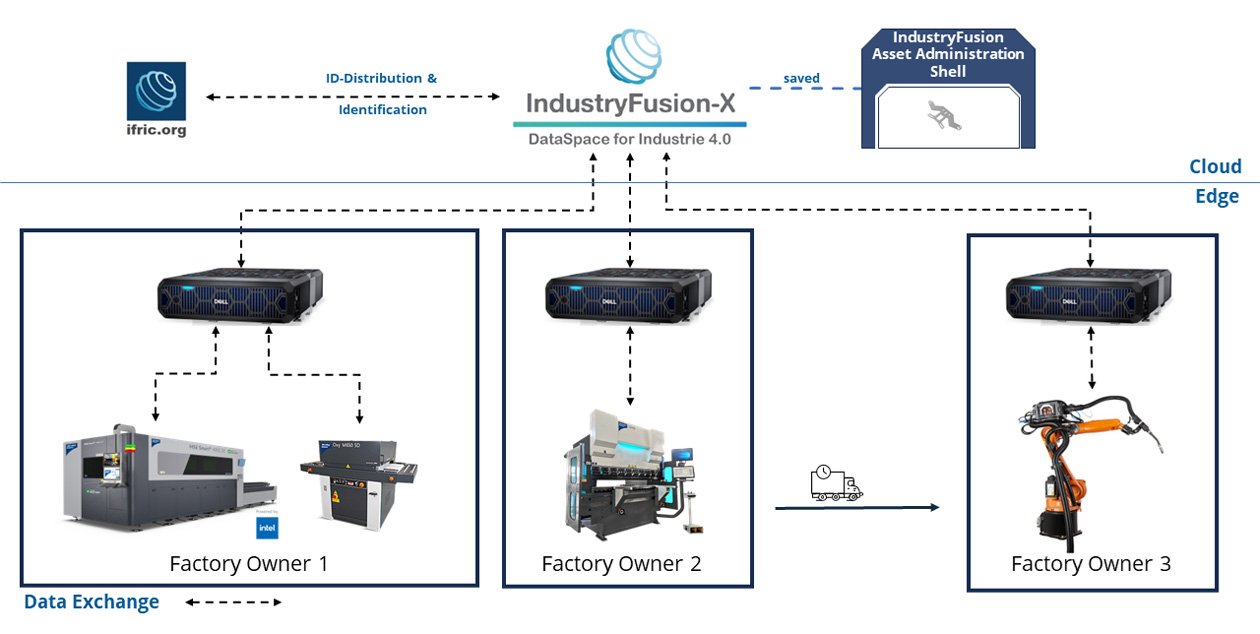
Every company, whether manufacturer or factory operator, has its own Factory Server. The Factory Server is connected at edge level to the individual machines and electrical devices such as a laser cutting system. Via IndustryFusion-X as a cloud-based data room and the connection to the Factory Server, a network of different companies is created. With the connection to IndustryFusion-X and the associated allocation of identification numbers by the IFRIC, unique identification takes place. This globally unique identification creates a digital twin stored in an administration shell with which all manufacturing and production processes as well as, for example, material properties or documents are linked.
Benefits
The storage of production and manufacturing data in the digital twin parallel to the individual process steps guarantees simple and direct data availability for the asset to be produced. The administrative effort for data preparation and processing is eliminated by the standardised communication between the factory server and the cloud-based data room. Every factory operator, whether processing company or customer, has access to all data along the production and manufacturing process.